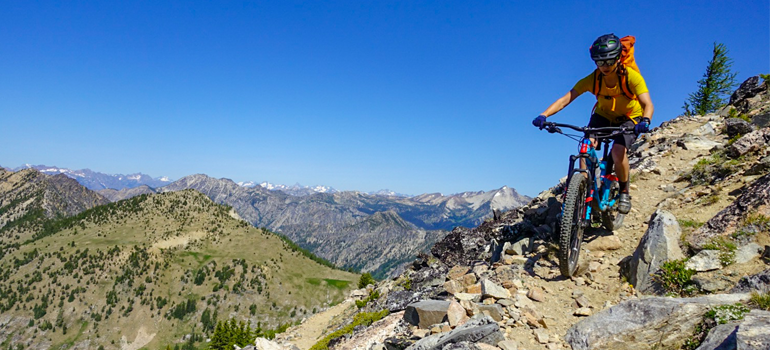
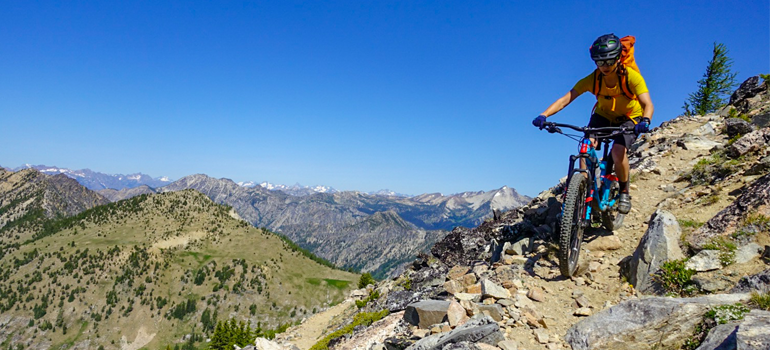
Economics alumna Saravie Brewer mountain biking.
Saravie Brewer’s career combines her formal training in economics with her love of the outdoors. Brewer (MA’10) works as the Project and Process Improvement Manager, Supply Chain, for Arc’teryx Equipment, an outdoor apparel and sporting goods company founded in North Vancouver. It’s here where the avid mountain biker applies data-driven models to recommend and implement projects that improve operational efficiency.
Brewer has worked at Arc’teryx for more than four years, and is in her fourth role for the company.
How do you describe your role at Arc’teryx Equipment?
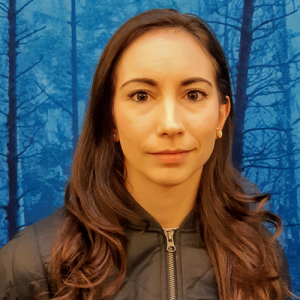
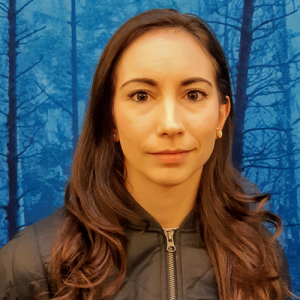
Saravie Brewer
I am tasked with coming up with various solutions to improve efficiency in the company’s supply chain. This involves all of the steps involved in getting, for example, a shell jacket all the way to the final customer, from procuring raw material to warehousing and delivery, and making sure it’s available in the right channels at the right time. Most people may not be aware of the amount of planning involved in getting the jacket they just bought into their hands – whether they bought it via an Arct’eryx store, a specialty retailer, or from our website.
Many of the steps along the way rely heavily on how we forecast for the demand, like how products each warehouse will need, in a certain style, colour, size, and at what time. These forecasts drive much of the work done by our teams, for example, negotiating for long-term capacity with factories, warehouses and raw material vendors. Demand can be a fun challenge to forecast, due to factors like new technology, product evolution, weather, and competition, to name a few. Supply can be hard to adjust because of long lead times, and factory and raw material constraints.
There is an important trade-off between building inventory and the risk of selling out and losing sales. I work with teams across the company to evaluate different strategies related to demand forecasting, sales and operations planning, and inventory optimization., We’re always trying to identify how we can optimize what we’re doing with the resources at hand and how we can make the whole process as efficient as possible.
How has an economics background helped you in your current position?
Some of the most valuable ideas I learned studying economics were optimizing based on constraints, decision-making under uncertainty, and program evaluation. Economics provides you with a real, structural way of thinking about problems, which can be applied to answer almost any question. My current position provides ample opportunity to apply some of these ideas. Unlike in the problem sets you solve in class as a student, working in the real world, especially in the apparel industry, you never do solve anything perfectly. Outside the classroom, you learn to get creative and work with imperfect data.
Why did you study economics at UBC?
I did my undergraduate degree in finance at Simon Fraser University and the introductory economics courses I took when I started were eye-opening. I loved the new, structured, ways of trying to understand the world. When it came time to graduate, I decided that economics was the route for me. When it came to graduate schools in Canada for economics, UBC was at the top of the list for me because of its great reputation.
What was the best part about studying at UBC?
The best part was the people. To this day, some of my closest friends are my fellow MA students. Everyone is living in various parts of the world, but we keep in close contact.